How Do Grease Lubrication Systems Enhance Equipment Longevity?
- Lubsa Multilub Systems
- Aug 8, 2023
- 2 min read
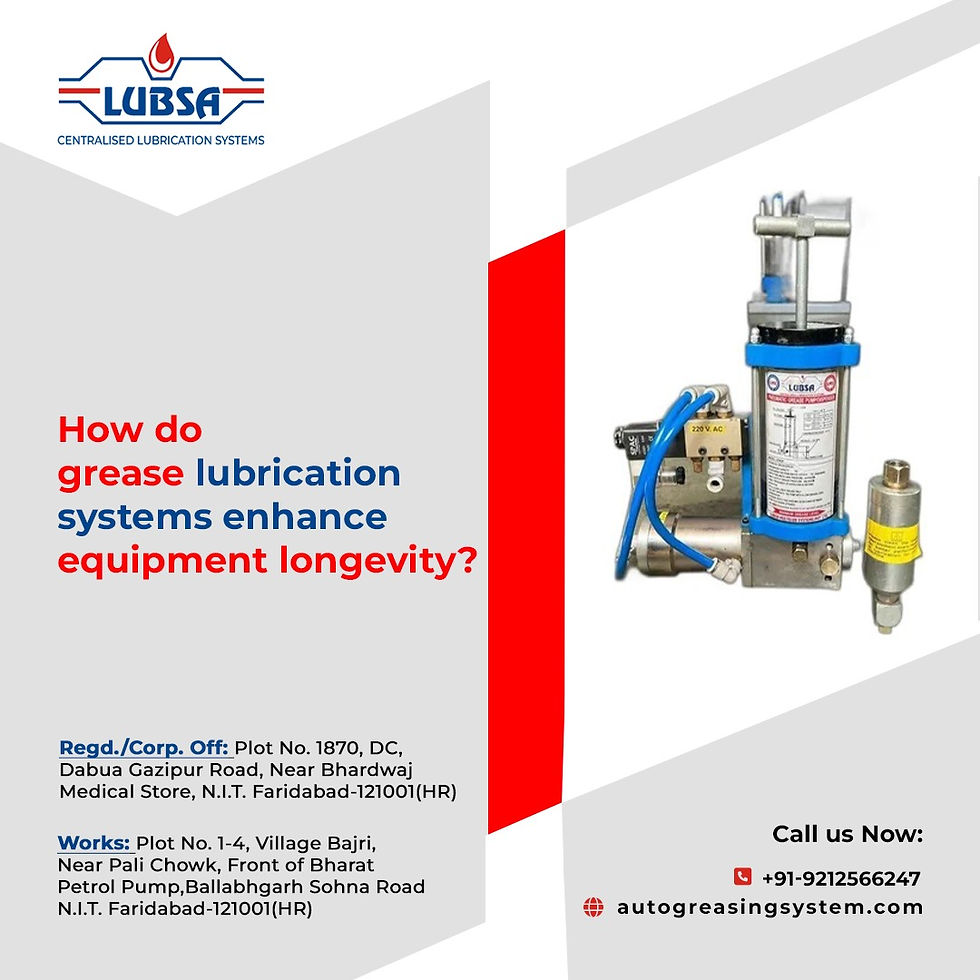
Grease lubrication systems are essential for increasing the life of machinery and equipment. These systems are intended to provide a steady flow of grease to essential components, minimizing friction, preventing wear and tear, and eventually adding to the equipment's overall lifetime. In this post, we'll look at how grease lubrication systems function and how they help equipment last longer.
How is Greasing Lubrication System Used to Enhance Equipment Longevity?
Recognizing grease lubrication systems
The administration of a semi-solid lubricant known as grease to the moving elements of equipment is known as grease lubrication. Grease is a combination of oil and a thickening agent that is frequently supplemented with additives to improve performance. Grease lubrication systems are designed to provide grease to specific places within machinery, ensuring that the components run smoothly and effectively.
Friction and wear reduction
The inherent enemy of machinery is friction. Friction creates heat and promotes surface wear when components move and come into contact. Grease lubrication systems function by creating a protective layer between moving parts. This layer of grease works as a barrier, limiting direct contact and friction between surfaces. This reduction in friction reduces the heat created during operation and saves parts from prematurely wearing down, potentially extending the equipment's lifespan greatly.
Keeping corrosion and contaminants at bay
Machinery is frequently subjected to a variety of environmental conditions, including dampness and pollutants. Grease lubrication systems give an extra degree of security by forming a barrier that keeps moisture from coming into direct contact with metal surfaces. Furthermore, grease includes corrosion-resistant compounds.
Maintaining constant lubrication
Grease lubrication systems are designed to give a consistent and accurate amount of grease to certain lubrication sites. This uniformity is critical because it guarantees that all components receive the lubrication they require to function properly. Uneven lubrication can cause areas of high wear and poor protection, reducing the lifespan of the equipment. Grease lubrication systems aid in the maintenance of consistent lubrication, even in difficult-to-reach or high-speed locations.
Keeping downtime and maintenance to a minimum
Downtime for maintenance or repairs on equipment may be costly and inconvenient to business. Grease lubrication systems assist in reducing such downtime by continuously lubricating essential components. Lubrication jobs demand less manual involvement with regular and automated lubrication. This proactive approach not only increases the equipment's lifespan but also decreases costs.
Choosing the Best Grease and Maintaining It
Choosing the right grease for the job is critical for maximizing equipment lifespan. Engineers and operators can use grease lubrication systems to select greases with the appropriate viscosity and additives for the equipment's needs. These systems frequently have programmable settings that allow users to vary the lubrication frequency based on the operational demands of the gear.
Conclusion:
Greasing System Suppliers supply grease lubrication systems in the realm of machinery and equipment, which cannot be overemphasized. These systems considerably increase equipment lifespan by reducing friction, eliminating wear, corrosion, and contamination, and guaranteeing constant lubrication.
They contribute to smoother operations, fewer maintenance requirements, and less downtime, eventually contributing to increased efficiency and cost savings for sectors that rely on the durability and effectiveness of their products.
Comentarios