Essential Grease Lubrication Systems for Manufacturing Efficiency
- Lubsa Multilub Systems
- Aug 8, 2024
- 3 min read
The reliability and efficiency of machines are critical in the fast-paced manufacturing industry. Proper lubrication is one of the key elements that guarantee these qualities. Because of their dependability and efficiency, the Grease Lubrication System is particularly significant among lubrication techniques. This blog explores the advantages and functions of grease lubrication systems in the manufacturing industry.
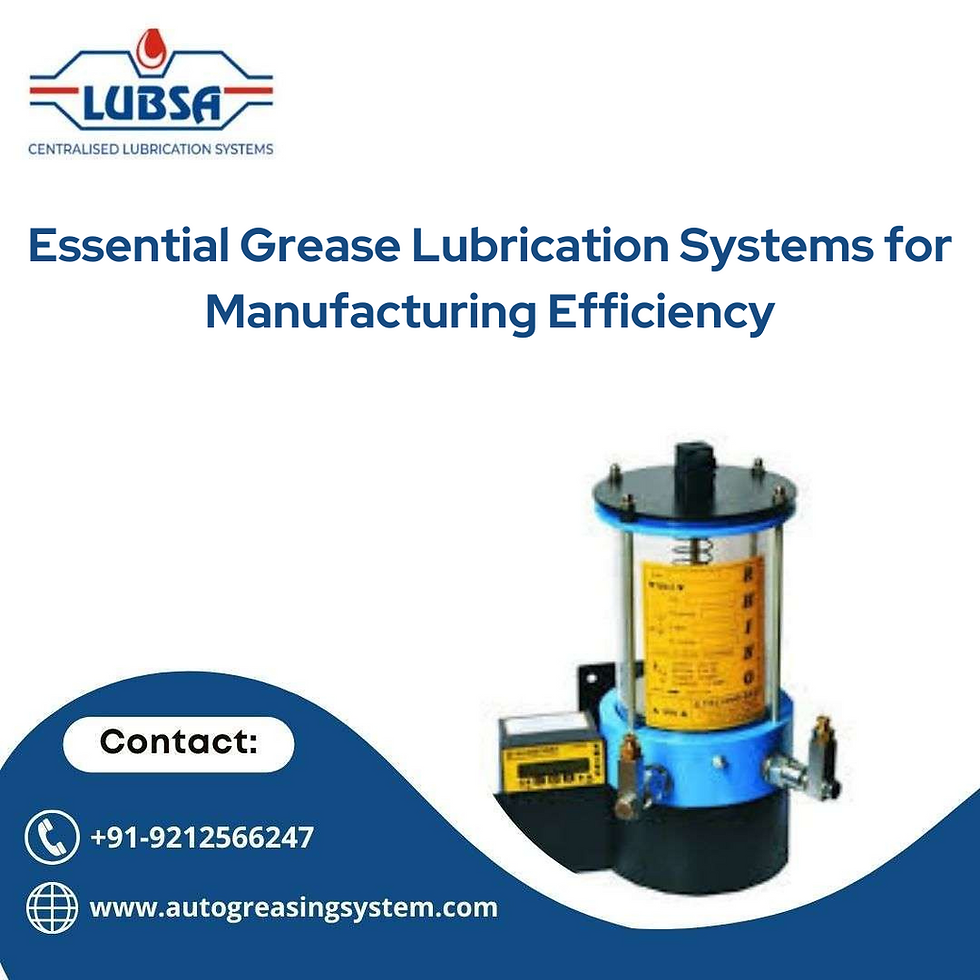
What is a Grease Lubrication System?
The efficient and smooth functioning of machine components is ensured by the grease lubrication system that is meant to supply grease to them. Grease is made up of a basic oil, thickener, and additives; unlike oil, which flows smoothly, grease is a semi-solid lubricant. Because of its specific composition, it works particularly well in conditions where relubrication is difficult or rare and provides long-lasting lubrication. Choosing a trustworthy Grease Lubrication Systems Manufacturer to collaborate with is essential for businesses looking for reliable solutions.
How Does a Grease Lubrication System Work?
The following elements are frequently encountered in grease lubrication systems:
Grease Reservoir: Stores grease before it is distributed.
Pump: Moves grease from reservoir to delivery points.
Distribution Network: a system of hoses or pipes that move grease to the lubrication locations.
Control Units: Adjust the grease's pressure and flow to ensure the best possible supply.
Grease Reservoir: Stores grease before distribution.
Lubrication Points: The parts of the machine that need to be lubricated, like the chains, gears, and bearings.
Grease from the reservoir is forced through the distribution network and into the lubrication points by the pump when it is turned on. To maintain efficient lubrication and avoid over-lubrication, which can result in grease waste and equipment damage, the control units make sure that the proper amount of grease reaches every point.
Benefits of Grease Lubrication Systems
Enhancing the Efficiency of Machinery
Smoother operation and enhanced performance are the results of proper lubrication, which reduces friction and wear between moving parts. This ensures that equipment operates effectively, resulting in the production of higher-quality products and reduced.
Extended Life of Equipment
Grease lubrication systems extend the life of machine parts by reducing wear and friction. Over time, this lowers the need for replacements and repairs, which results in significant cost savings.
Reduce Maintenance Costs
The requirement for human lubrication is decreased by grease lubrication systems, which automate the lubrication process. This ensures accurate and consistent lubrication, reducing maintenance expenses and saving time. Using a reliable grease systems supplier will help you get solutions specifically tailored to your maintenance requirements.
Enhanced Security
Manual lubrication frequently necessitates stopping machinery, which could be dangerous. Continuous operation is made possible by automated grease lubrication systems, which improve worker safety by minimizing the need for maintenance staff to handle moving parts.
Adaptability
Systems for lubricating machinery with grease are appropriate for a variety of uses, including large-scale industrial gear. They are adaptable to the unique lubricating requirements of various manufacturing processes.
Applications of Grease Lubrication Systems
Several different production sectors use grease lubrication systems, including:
Automotive: Ensuring that machines and assembly lines run smoothly.
Food and Drink: supplying reliable lubrication in conditions with high moisture content.
Textile: Reducing wear and friction in fast-moving machinery.
Mining: Preserving large equipment under challenging circumstances.
Aerospace: Making sure vital components are precise and dependable.
Choosing the Right Grease Lubrication System
The following aspects should be considered when choosing a grease lubrication system:
Machinery Type: Different types of machinery require different lubricants.
Operating Environment: Elements including humidity, temperature, and pollutant exposure.
Maintenance Schedule: the frequency of lubrication and maintenance intervals.
Grease Type: The grease's compatibility with the equipment and working environment.
You can ensure you have the greatest system possible, customized to your unique requirements, by working with a reputable grease lubrication systems manufacturer or grease systems supplier.
Conclusion
Systems for grease lubrication are essential to the manufacturing industry because they prolong the life of machinery, improve safety, save maintenance costs, and extend machinery performance. Manufacturers may optimize their operations and get more efficiency by making informed decisions by knowing the significance and advantages of these systems.
Purchasing a dependable grease lubrication system is essential for continuously operating, optimizing production, and ensuring the safety and efficiency of your entire manufacturing process. It goes beyond simple machinery maintenance. Deal only with reliable Grease Lubrication Systems Manufacturers and Greasing Systems Suppliers for optimal outcomes.
コメント